Rapid prototyping is widely used in a wide variety of industries whenever industries need to launch a product for commercial purposes. Fast prototyping involves a diverse set of techniques to fabricate a product model that has to be launched commercially or used in any assembly line. Previously, fast prototyping was mostly used for designing and scaling purposes in the auto industry. Now, it has been expanded to robotics, aviation, medical equipment, electronics, and virtually any industry you can think of. This means that getting fast prototyping services has become part and parcel of any industry trying to beat the competition. But prototypes are made using a variety of techniques, and each of them has its pros and cons. Let’s see them one by one.
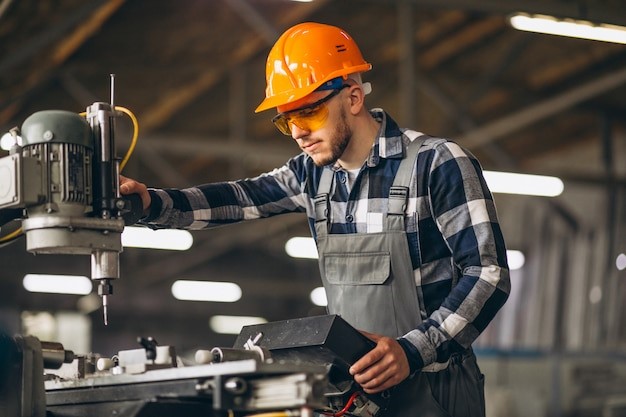
Ways To Build Prototypes
Subtractive Manufacturing (CNC Machining)
Computer Numerical Control or CNC rapid prototyping is a method in which pre-programmed software controls the movement of the machines to design the prototype. The prototype is built when the software treats the required material using different techniques like milling, grinding or tuning, etc.
Rapid Sheet Metal Fabrication
Sheet metal fabrication involves turning a plain metal sheet into the functional parts of a product. This process involves rapid prototyping services like molding, bending, cutting and punching to produce the desired prototype.
Vacuum Casting
Fast prototyping via vacuum casting occurs when silicone molds are used under a vacuum to make plastic or rubber components for fabricating a prototype. It’s a highly efficient process since no air is trapped under a vacuum, thereby giving you the smooth surfaces of a prototype.
Reaction Injection Molding
In this technology, multiple liquids interact with each other in low-pressure and low-temperature chambers. These liquids undergo polymerization to form a mold, which is eventually injected into the material supposed to be converted into the